Fasteners and Machining: Enhancing Toughness and Efficiency in Production
Fasteners and Machining: Enhancing Toughness and Efficiency in Production
Blog Article
Grasping the Art of Fasteners and Machining: Developments and Best Practices
In the realm of commercial production and design, the mastery of fasteners and machining is a cornerstone of ensuring architectural honesty, capability, and durability in different applications. As technology advances and demands for efficiency and precision rise, remaining abreast of the newest developments and best techniques in fastening and machining becomes vital. From the evolution of fastening modern technologies to the ins and outs of selecting one of the most appropriate materials, the landscape of modern-day manufacturing is continuously progressing. Join us as we explore the current innovations and dig into the nuanced globe of mastering bolts and machining, discovering crucial insights and methods that can raise your approach to design services.
Evolution of Attachment Technologies
Throughout the industrial revolution and right into the modern-day era, the advancement of securing modern technologies has been marked by constant advancements in effectiveness and dependability. Bolts, such as bolts, screws, and rivets, play an essential role in various markets, including vehicle, aerospace, construction, and electronics. The requirement for stronger, a lot more sturdy, and easier-to-install attachment solutions has driven development in the field.
One considerable growth has been the shift in the direction of accuracy machining strategies to develop bolts with greater resistances and premium efficiency. This change has actually made it possible for suppliers to generate bolts that satisfy rigorous high quality standards and deal enhanced resistance to rust and tiredness.
In addition, the intro of sophisticated products, such as titanium alloys and composites, has revolutionized the capabilities of bolts. Fasteners and Machining. These products give remarkable strength-to-weight ratios, making them ideal for applications where reducing weight is critical without jeopardizing structural stability
Developments in Machining Techniques
In the realm of industrial manufacturing, the continuous evolution of machining approaches has actually led the means for unprecedented accuracy and effectiveness in the production of bolts. One of the significant advancements in machining approaches is the use of Computer Numerical Control (CNC) modern technology. CNC makers provide unmatched precision and repeatability by permitting automated control of machining devices. This exact control enables suppliers to develop complicated and detailed fastener styles with simplicity.

In addition, the adoption of multi-axis machining centers has allowed simultaneous cutting operations from various angles, further boosting effectiveness and reducing manufacturing times. By using these innovative machining approaches, suppliers can satisfy the increasing need for high-grade fasteners while maintaining cost-effectiveness in their procedures.
Choosing the Right Bolt Materials
Picking the suitable product for fasteners is an important choice that significantly affects the performance and durability of the assembled parts. When choosing the ideal fastener material, several aspects must be taken into consideration to guarantee the durability and dependability of the end product. The product selected ought to work with the environmental problems the bolts will be revealed to, such as temperature level variations, dampness degrees, and destructive aspects.
Typical products used for bolts consist of stainless steel, carbon aluminum, titanium, and steel, each offering one-of-a-kind homes that match various applications. Stainless-steel, as an example, is understood for its rust resistance, making it ideal for aquatic or exterior settings. Carbon steel is an affordable option suitable for many general-purpose applications. Aluminum is lightweight and commonly made use of in sectors where weight is a crucial element. Titanium, on the other hand, is remarkably solid and corrosion-resistant, making it ideal for high-performance applications.
Enhancing Precision in Machining
Attaining ideal accuracy in machining is vital for ensuring the high quality and performance of machined elements. Accuracy in machining refers to the capacity to constantly generate parts within limited tolerances and with high accuracy. To improve accuracy in machining, producers use a variety of sophisticated strategies and innovations. One trick method is using Computer system Numerical Control (CNC) machines, which use superior accuracy and repeatability compared to typical manual machining techniques. CNC equipments are programmable and can execute intricate machining procedures with marginal human intervention, resulting in higher accuracy degrees.
In enhancement to CNC machining, the use of advanced cutting tools and tool owners can likewise dramatically enhance accuracy. Top notch cutting devices with innovative coatings reduce friction and wear, leading to much more accurate cuts and dimensional accuracy. Carrying out strict high quality control measures throughout the machining process, such as normal examinations and calibration of tools, assists preserve consistent precision degrees. By focusing on precision in machining, producers can achieve superior product high quality, tighter resistances, and boosted general performance of machined parts.
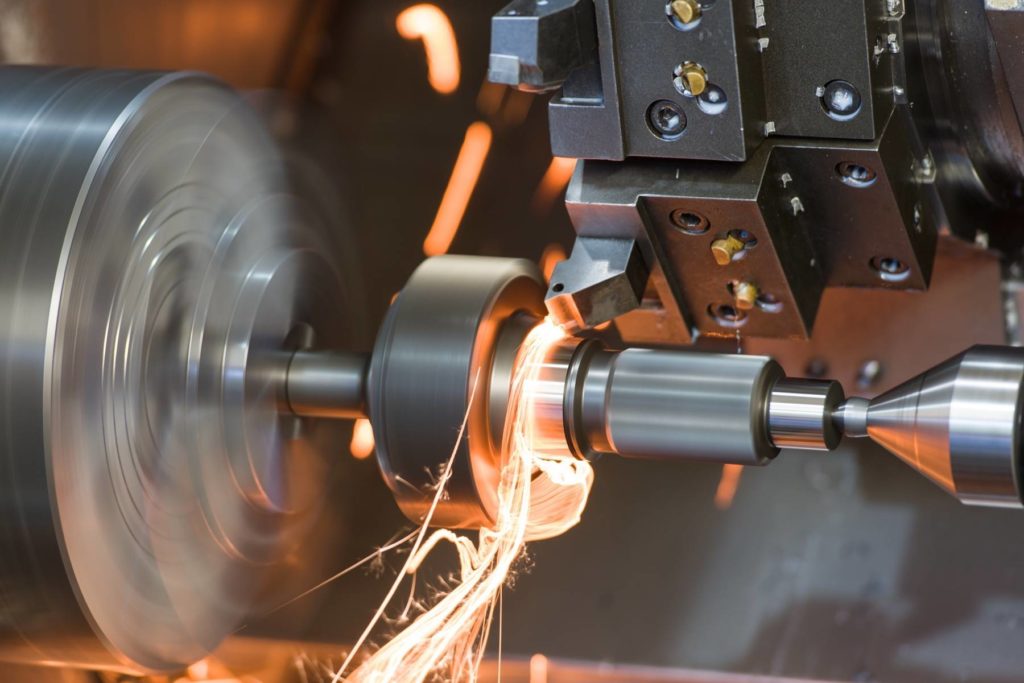
Best Practices for Fastener Installment
Accuracy in machining plays an important function in ensuring the integrity and durability of bolt installments. When read the full info here it comes to finest practices for bolt installment, one essential element is the correct selection of bolts check my site based on the particular application requirements.
Furthermore, guaranteeing that the bolt threads are complimentary and tidy of debris prior to setup is vital to attaining a secure and efficient connection. Using thread-locking compounds or washing machines can likewise enhance the stability of the fastener setting up. Normal assessments and upkeep of bolts post-installation are suggested to identify any type of prospective concerns at an early stage and stop costly repair work or substitutes in the future. By sticking to these ideal techniques, makers can enhance the integrity and performance of next their bolt installments.
Verdict
By picking the best fastener materials and enhancing precision in machining, suppliers can achieve optimal outcomes in their operations. Overall, understanding the art of bolts and machining includes continuous advancement and adherence to finest methods.
In the world of industrial production, the continual evolution of machining approaches has actually paved the way for unmatched accuracy and performance in the manufacturing of bolts.Accuracy in machining plays a vital role in ensuring the dependability and durability of fastener setups. When it comes to finest methods for fastener installation, one essential aspect is the proper choice of bolts based on the specific application needs. By selecting the best fastener materials and boosting accuracy in machining, producers can accomplish optimum results in their procedures. Overall, grasping the art of bolts and machining involves constant technology and adherence to ideal practices.
Report this page